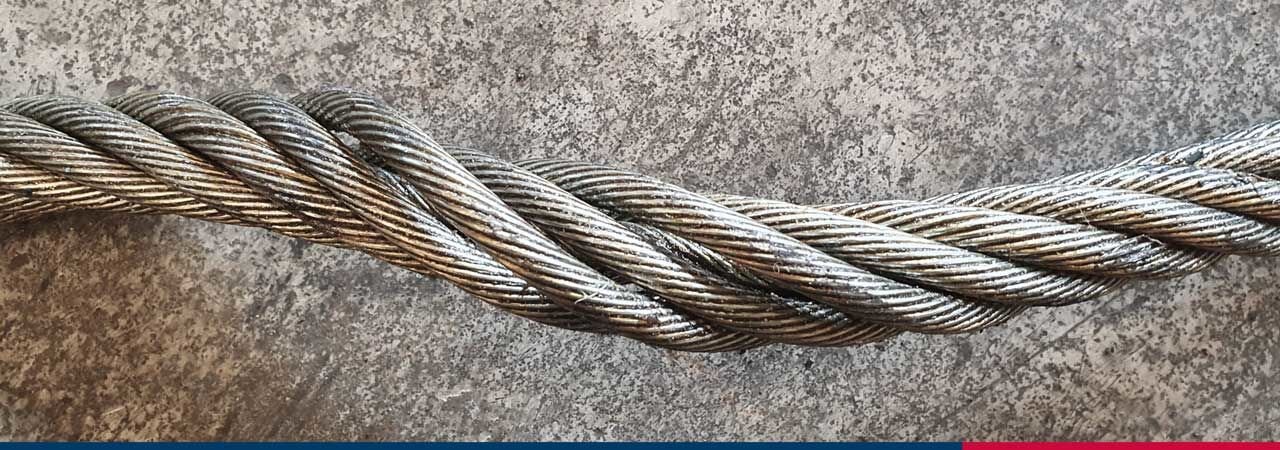
Inspection of steel wire ropes
Examination of steel wire rope before use
During examination of steel wire ropes attention should be made specifically to the parts of the rope that are, known from experience, to be exposed to wear and damage.
Wear, broken wires, distortion and corrosion are the most common visible signs of deterioration.
Wear is a normal feature of rope service and the correct rope construction ensures that it remains a secondary aspect of deterioration. Correct lubrication of the rope may help to reduce both outer and inner wear.
Broken wires are normal features of rope service towards the end of the rope's life, resulting from bending fatigue and wear. The local break up of wires may indicate some mechanical fault in the equipment. Correct lubrication in service will increase fatigue performance.
Individual broken wires shall be attended to by removing the wire, see figure.
Distortions are usually as a result of mechanical damage, and if severe, can considerably affect rope strength.
Corrosion, both outer and inner, indicate unsuitable grease. Pitting on the external wire surface can result in broken wires. Inner corrosion occurs in some environments when lubrication is inadequate or of a unsuitable type. A reduction in rope diameter will frequently indicate this condition, but confirmation can only be made by an internal examination of the rope.
WARNING! Do not cut the wire, bend it until it breaks close to the inside of the strajd. This reduces the risk of the ends of wires sticking out of the rope.
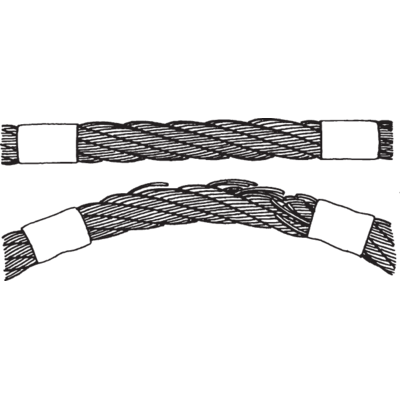
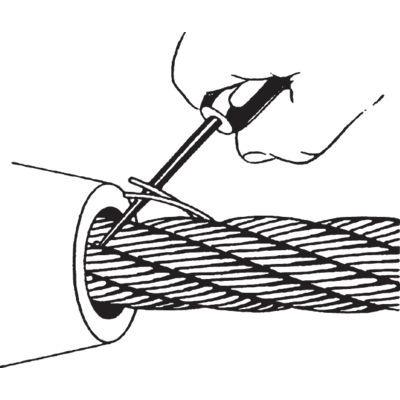
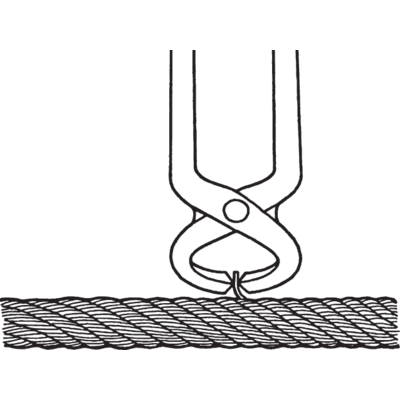
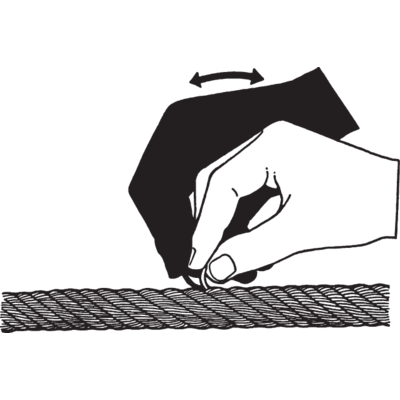
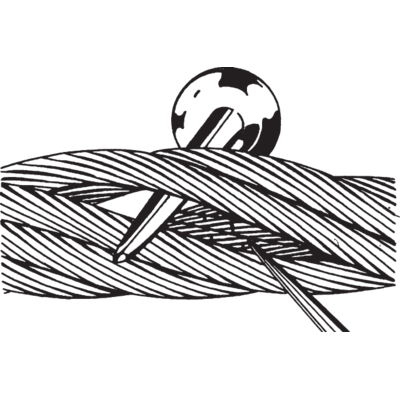
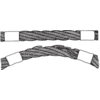
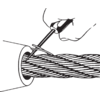
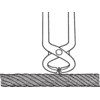
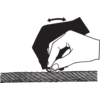
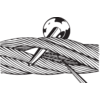
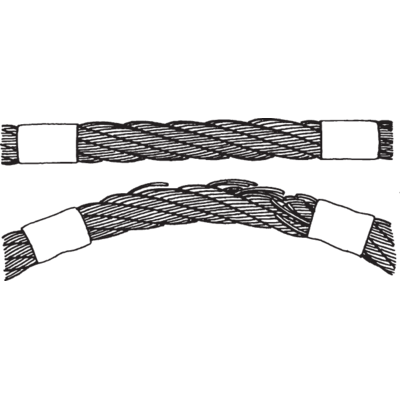
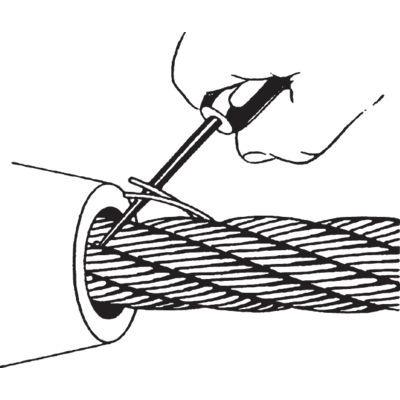
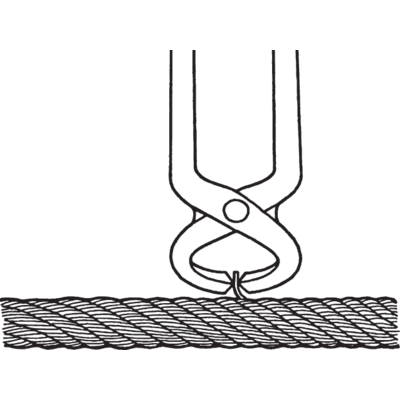
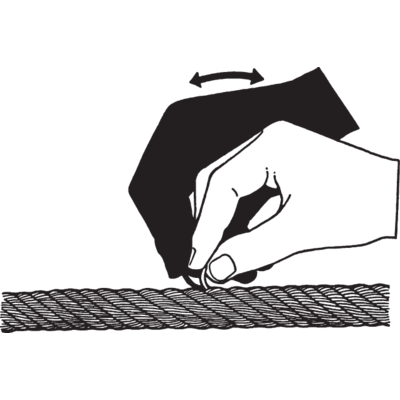
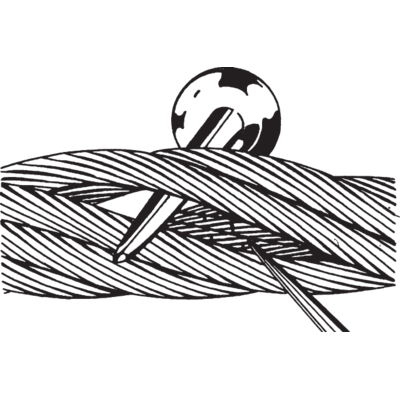
Steel wire rope rejection criteria
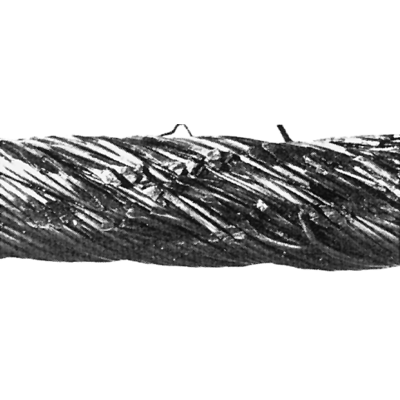
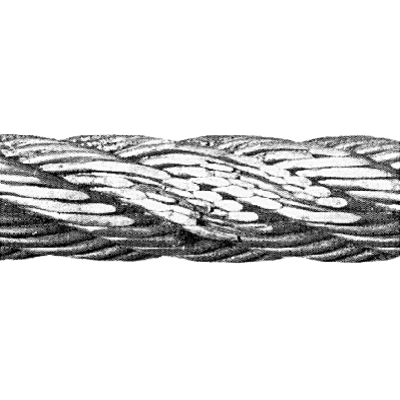
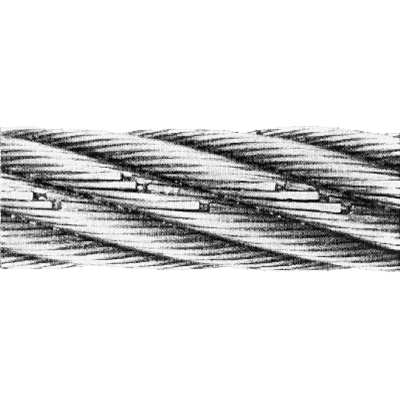
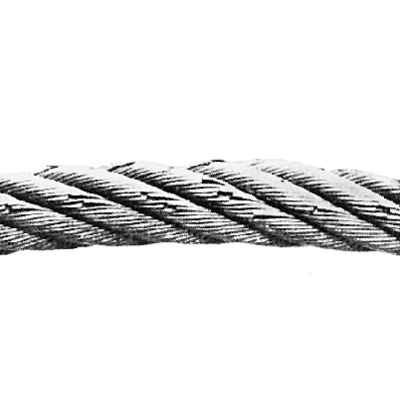
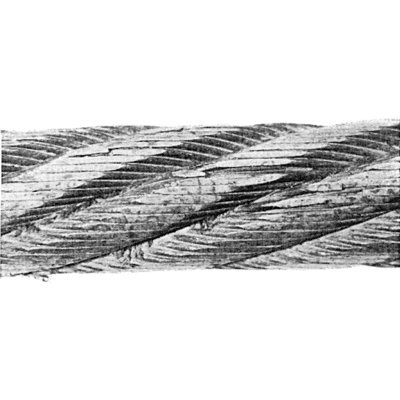
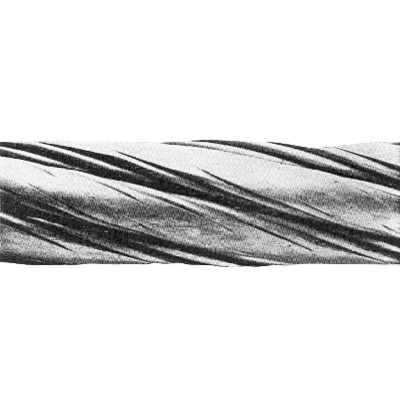
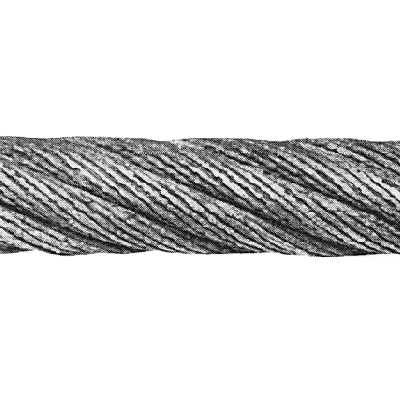
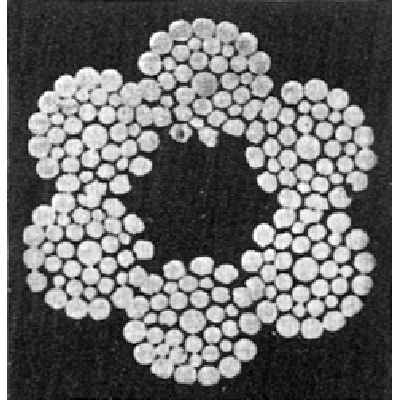
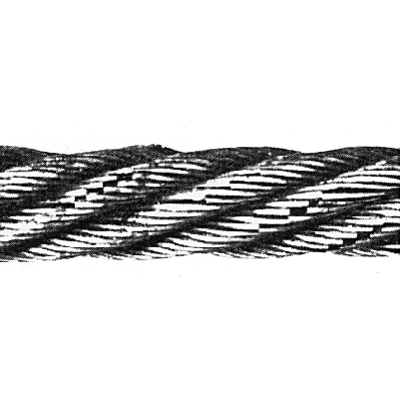
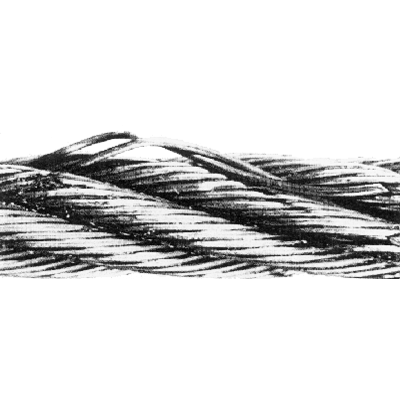
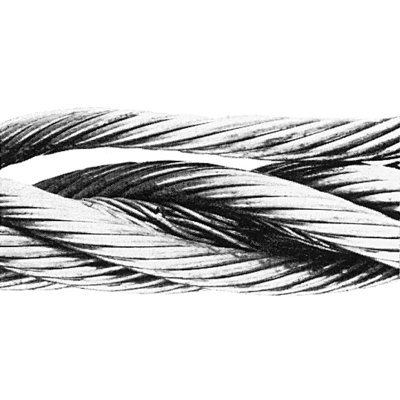

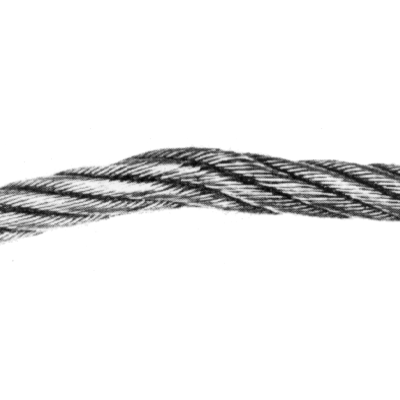
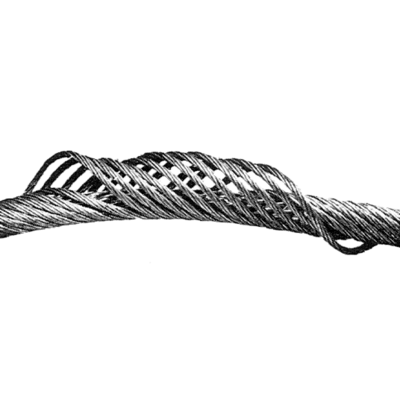
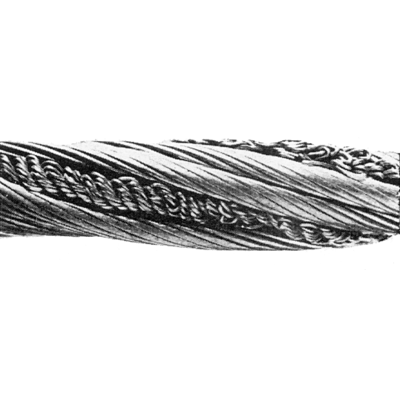
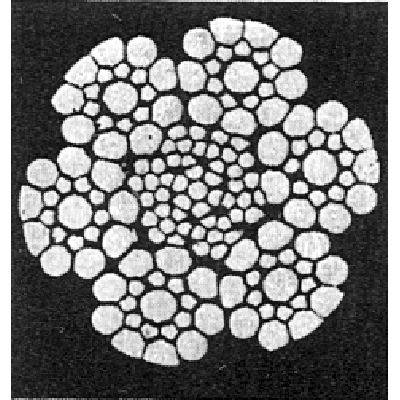
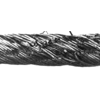
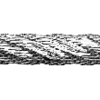
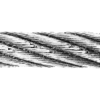
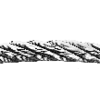

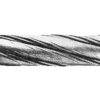
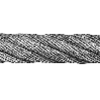
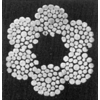

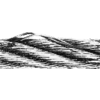
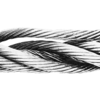
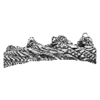
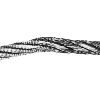
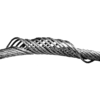
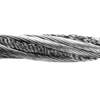
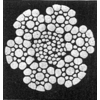
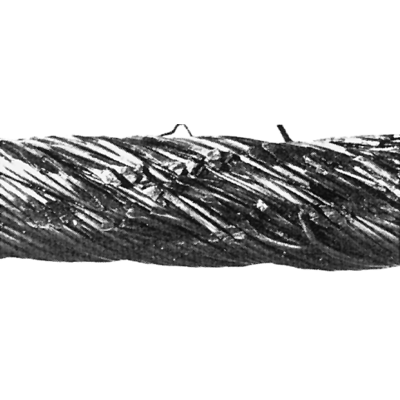
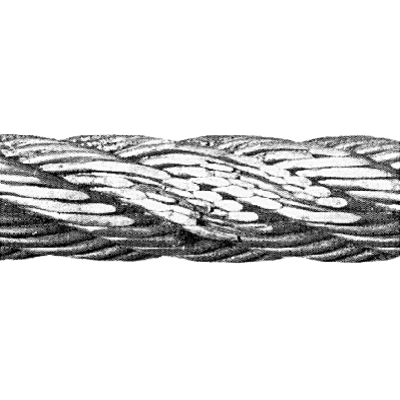
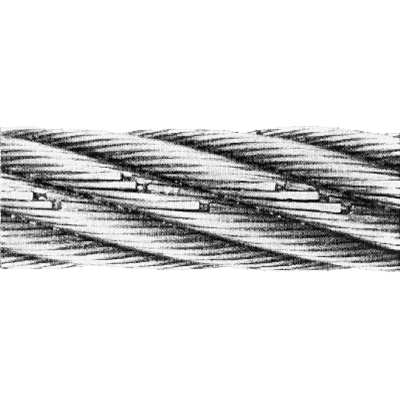
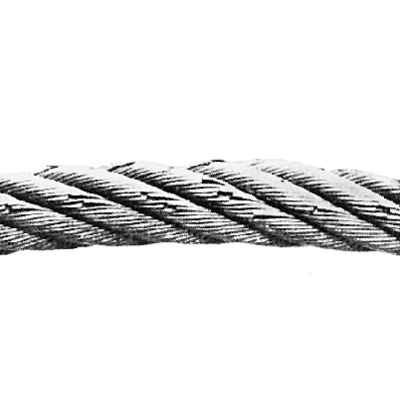
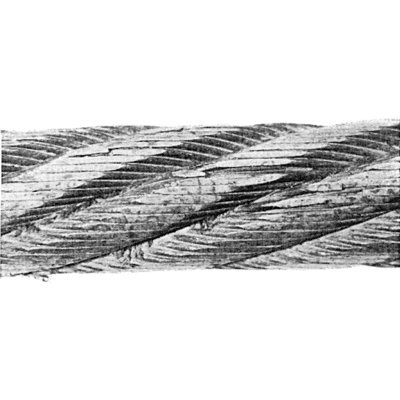
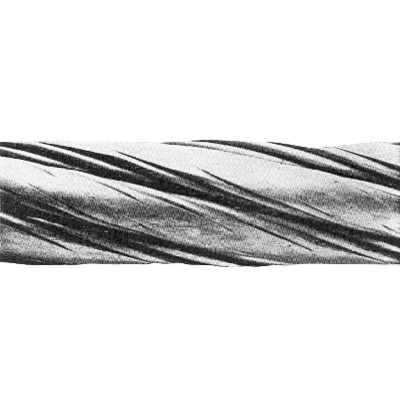
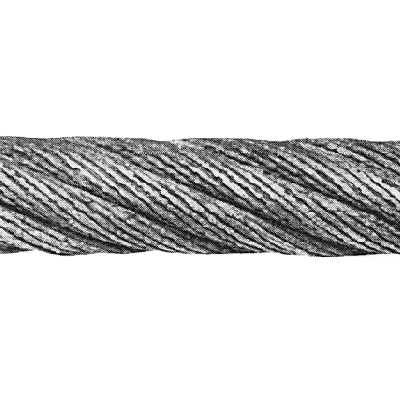
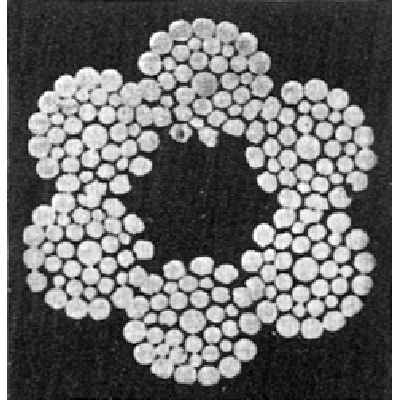
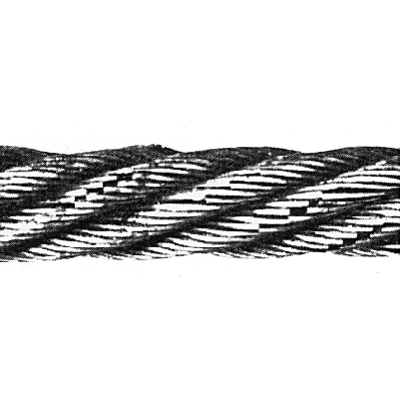
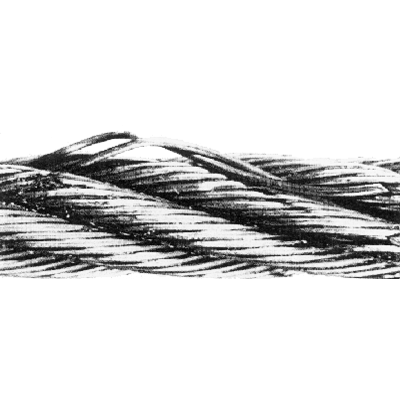
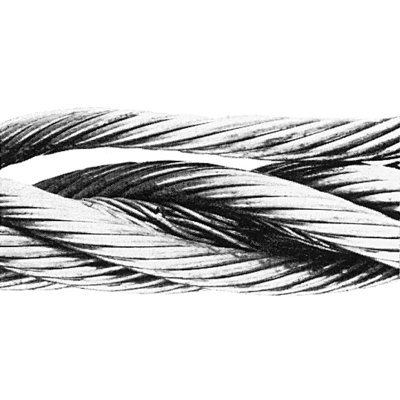

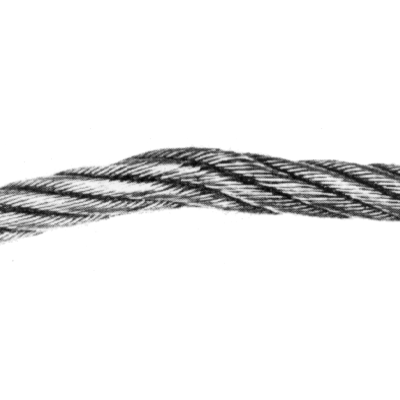
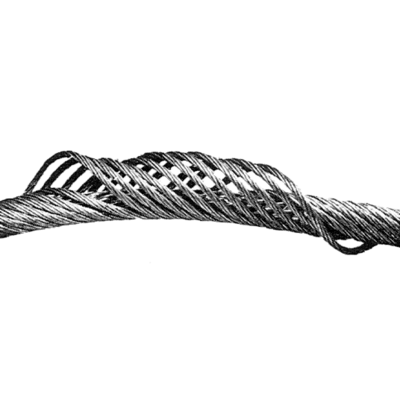
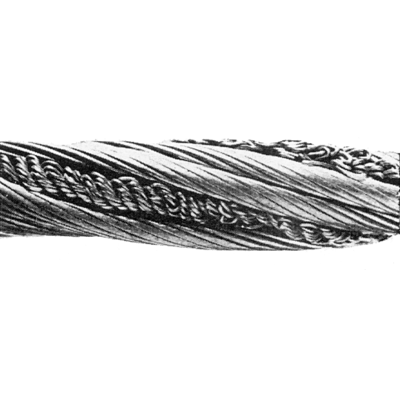
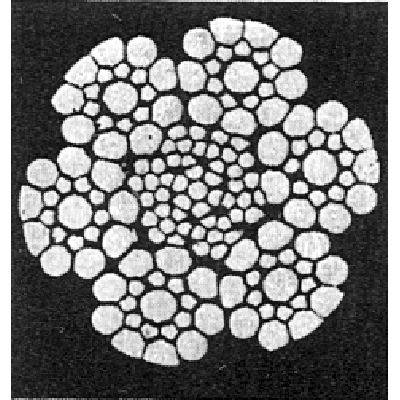
Do you have any questions?
If you have any additional questions, please contact us and we will answer you.